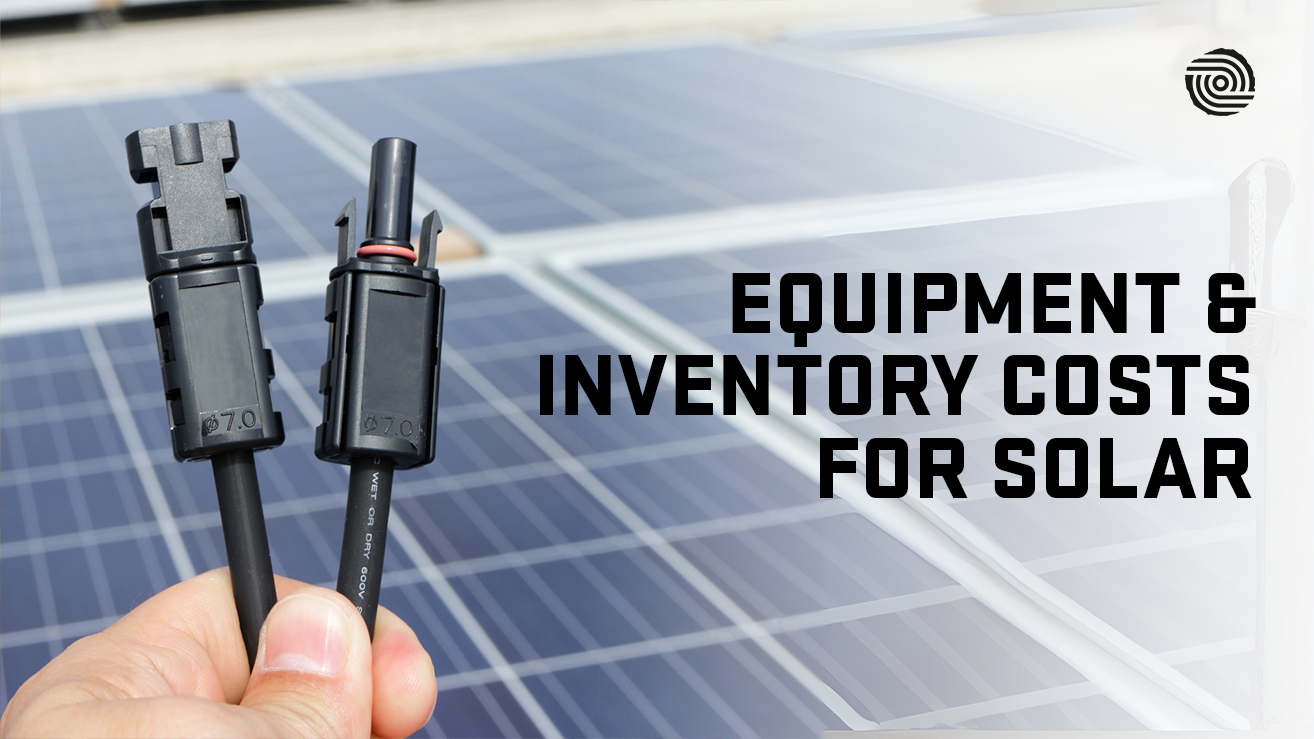
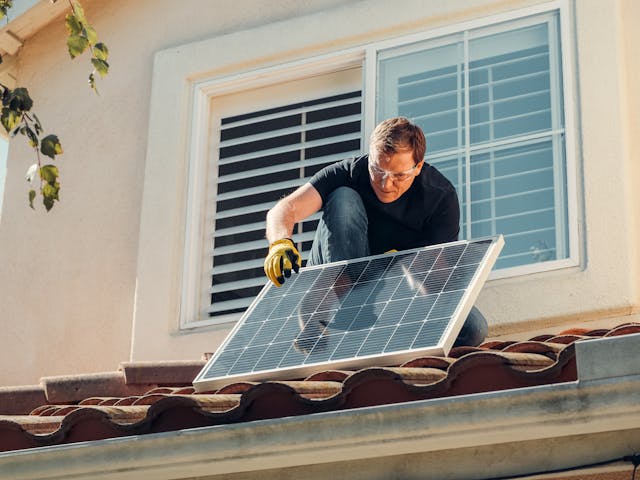
The solar energy sector has experienced explosive growth, with global installations reaching record highs year after year. However, behind every successful solar project lies a complex web of equipment procurement, inventory management, and cost control strategies. Effective solar inventory management has emerged as a critical success factor that can make or break a project's profitability and timeline. From photovoltaic panels and inverters to mounting systems and electrical components, managing the vast array of equipment required for solar installations presents unique challenges that demand specialized approaches and tools.
Solar companies today face mounting pressure to deliver projects on time and within budget while maintaining quality standards. Poor inventory management can lead to project delays, cost overruns, and reduced profit margins. This comprehensive guide explores the essential strategies, best practices, and metrics needed to master solar inventory management and optimize equipment costs for sustainable business growth.
What is Solar Inventory Management?
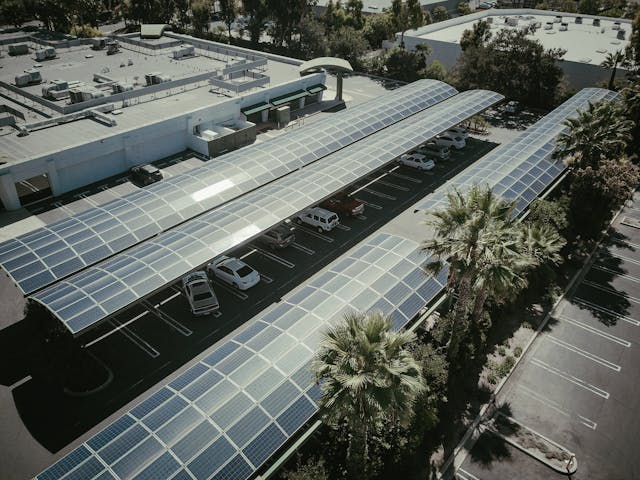
Solar inventory management refers to the systematic process of planning, procuring, storing, tracking, and distributing all equipment and materials required for solar energy projects. This encompasses everything from major components like solar panels, inverters, and mounting systems to smaller items such as connectors, cables, fuses, and safety equipment. The process involves coordinating with multiple suppliers, managing storage facilities, tracking inventory levels, and ensuring timely delivery to project sites.
Unlike traditional inventory management, solar inventory management must account for the unique characteristics of solar equipment, including varying sizes, weights, and storage requirements. Solar panels, for instance, require specific handling procedures and climate-controlled storage to prevent damage. Additionally, the industry's project-based nature means inventory must be allocated to specific installations, often across multiple locations and timeframes.
Effective solar inventory management systems integrate procurement planning, supplier relationship management, warehouse operations, and logistics coordination. Modern solutions leverage technology such as RFID tracking, barcode scanning, and cloud-based inventory management software to provide real-time visibility into stock levels, equipment locations, and project requirements. This technological integration enables solar companies to optimize their inventory levels, reduce carrying costs, and improve project delivery timelines.
Why is Solar Inventory Management Important?
Solar inventory management plays a pivotal role in determining project profitability and operational efficiency. The solar industry operates on typically thin margins, making cost control essential for sustainable business operations. Proper inventory management directly impacts cash flow by reducing tied-up capital in excess inventory while ensuring sufficient stock to meet project demands.
Project timeline adherence is another critical factor. Solar installations often face strict deadlines driven by utility interconnection schedules, permit expiration dates, and seasonal weather considerations. Equipment shortages or delays can cascade through project schedules, resulting in costly delays and potential contract penalties. Effective inventory management ensures the right equipment is available at the right time, maintaining project momentum and client satisfaction.
Quality control represents another significant benefit of structured inventory management. Solar equipment requires careful handling and storage to maintain performance specifications and warranty coverage. Proper inventory systems track equipment provenance, storage conditions, and handling procedures, reducing the risk of damaged or compromised components reaching project sites.
Risk mitigation extends beyond individual projects to encompass broader business continuity. Supply chain disruptions, whether from natural disasters, geopolitical events, or market fluctuations, can severely impact solar companies. Strategic inventory management, including safety stock maintenance and supplier diversification, provides buffer against these uncertainties and enables continued operations during challenging periods.
7 Solar Inventory Management Challenges for Solar Companies
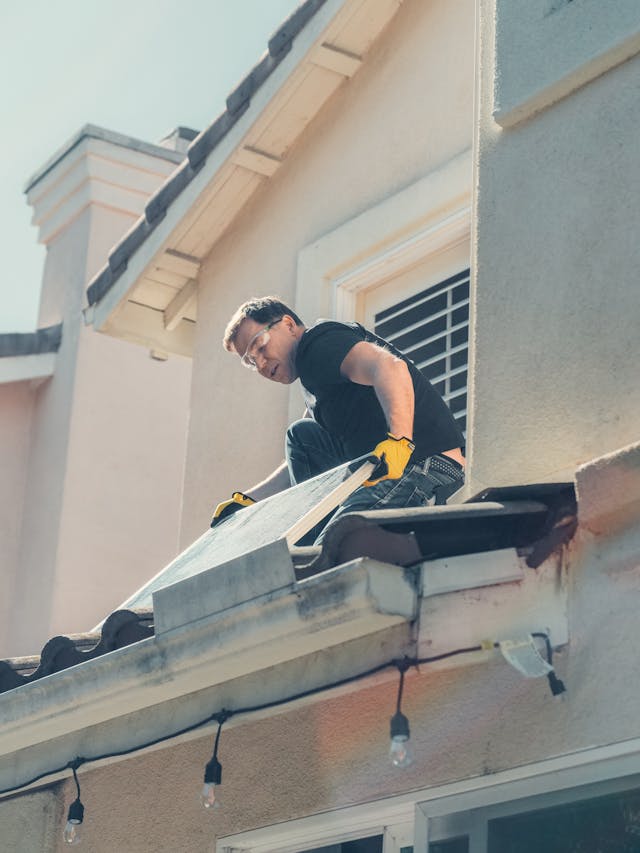
1. Complex Supply Chain Coordination
Solar projects require components from multiple suppliers, often spanning different countries and time zones. Coordinating deliveries from panel manufacturers in Asia, inverter suppliers in Europe, and mounting system providers domestically creates logistical complexity. Each supplier operates on different lead times, shipping schedules, and quality standards, making synchronization challenging.
2. Seasonal Demand Fluctuations
The solar industry experiences significant seasonal variations in installation activity, driven by weather patterns, utility incentive cycles, and year-end tax considerations. Companies must balance inventory levels to meet peak demand periods while avoiding excess stock during slower months. This cyclical nature makes demand forecasting particularly challenging.
3. Rapidly Evolving Technology
Solar equipment technology advances rapidly, with new panel efficiencies, inverter capabilities, and mounting innovations emerging regularly. Companies must balance maintaining current inventory levels with the risk of technological obsolescence. Outdated equipment may become difficult to sell or integrate into new projects, creating write-off risks.
4. Storage and Handling Requirements
Solar equipment presents unique storage challenges due to size, weight, and environmental sensitivity. Solar panels require significant warehouse space and careful handling to prevent damage. Inverters and electrical components need climate-controlled environments to maintain performance specifications. These requirements increase storage costs and complexity.
5. Project-Specific Equipment Allocation
Unlike retail inventory, solar equipment must be allocated to specific projects with defined specifications and timelines. This creates challenges in inventory pooling and flexibility. Equipment purchased for one project may not be suitable for another, limiting inventory utilization and increasing carrying costs.
6. Supplier Relationship Management
Solar companies must maintain relationships with multiple suppliers while negotiating favorable terms and ensuring reliable delivery. Balancing cost considerations with quality requirements and delivery reliability requires ongoing supplier evaluation and management. Single-source dependencies create vulnerability to supply disruptions.
7. Regulatory and Compliance Tracking
Solar equipment must meet various regulatory standards and certifications, including UL listings, IEC standards, and local electrical codes. Tracking compliance documentation and ensuring equipment meets project-specific requirements adds complexity to inventory management. Non-compliant equipment can result in project delays and additional costs.
How Does Solar Inventory Management Work?
Solar inventory management operates through a structured process that begins with comprehensive demand planning and forecasting. Companies analyze historical project data, current pipeline information, and market trends to predict future equipment requirements. This forecasting considers seasonal variations, technology trends, and supplier lead times to determine optimal ordering schedules and quantities.
The procurement phase involves supplier selection, contract negotiation, and purchase order management. Solar companies typically maintain relationships with multiple suppliers for each equipment category to ensure competitive pricing and supply security. Procurement teams coordinate delivery schedules to align with project timelines while optimizing shipping costs and warehouse capacity.
Upon receipt, equipment undergoes inspection and verification processes to ensure quality standards and specification compliance. Items are cataloged in inventory management systems using unique identifiers such as serial numbers or batch codes. This documentation enables traceability throughout the equipment lifecycle and supports warranty claims and quality control procedures.
Storage management involves organizing equipment in warehouse facilities with appropriate environmental controls and security measures. Inventory systems track equipment locations, quantities, and condition status. Advanced systems utilize barcode scanning or RFID technology to automate tracking and reduce manual errors.
Distribution management coordinates equipment movement from storage facilities to project sites. This includes packaging, shipping arrangement, and delivery scheduling. Inventory systems update stock levels in real-time as equipment is allocated to projects and shipped to installation sites.
Throughout this process, inventory management systems provide reporting and analytics capabilities that enable performance monitoring and optimization. These systems generate insights on inventory turnover, carrying costs, supplier performance, and equipment utilization rates.
Key Metrics for Measuring Solar Inventory Management Success
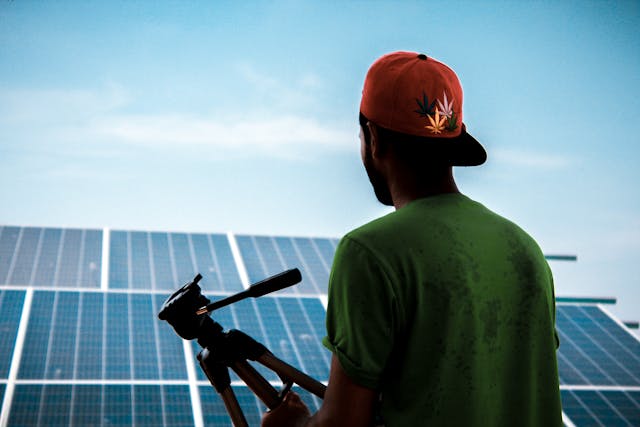
Inventory Turnover Ratio
This fundamental metric measures how efficiently inventory is converted into project installations. Calculated as the cost of goods sold divided by average inventory value, higher turnover ratios indicate more efficient inventory utilization. Solar companies typically target turnover ratios between 4-8 times annually, though this varies based on business model and market conditions.
Carrying Cost Percentage
Carrying costs encompass all expenses associated with holding inventory, including storage fees, insurance, financing costs, and obsolescence risks. This metric, expressed as a percentage of average inventory value, helps companies understand the true cost of inventory investment. Effective solar inventory management typically maintains carrying costs below 25% of inventory value.
Stockout Frequency
This metric tracks instances when required equipment is unavailable for project needs. Stockouts can cause project delays and customer dissatisfaction, making this a critical performance indicator. Leading solar companies maintain stockout frequencies below 2% through strategic safety stock management and supplier coordination.
Lead Time Variability
Measuring the consistency of supplier delivery performance helps identify reliability issues and optimize safety stock levels. Lower lead time variability enables more efficient inventory planning and reduces the need for excess safety stock. This metric is particularly important for international suppliers with longer and more variable lead times.
Equipment Utilization Rate
This metric tracks the percentage of purchased equipment that is successfully deployed in projects versus items that become obsolete or damaged. High utilization rates indicate effective demand forecasting and inventory management. Target utilization rates typically exceed 95% for major equipment categories.
Supplier Performance Metrics
Comprehensive supplier scorecards track delivery performance, quality metrics, and pricing competitiveness. These metrics enable data-driven supplier selection and relationship management decisions. Key performance indicators include on-time delivery rates, quality defect rates, and pricing stability.
Solar Inventory Management Best Practices for Cost Control
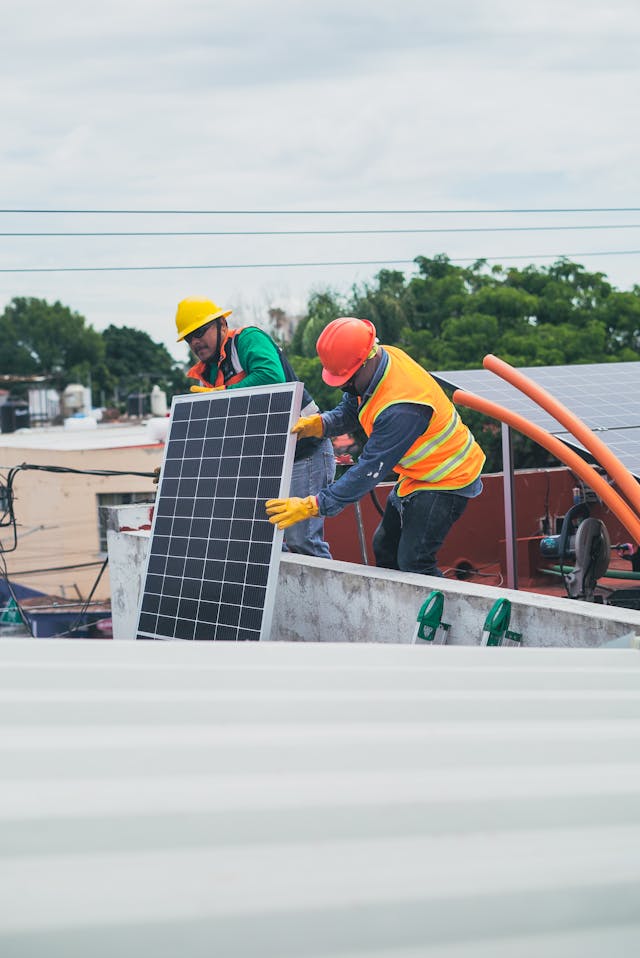
Implement Demand-Driven Planning
Successful solar inventory management begins with accurate demand forecasting based on project pipeline analysis and historical data. Companies should develop sophisticated forecasting models that consider seasonal patterns, technology trends, and market conditions. This approach minimizes excess inventory while ensuring adequate stock for project needs.
Optimize Safety Stock Levels
Strategic safety stock management balances the cost of holding inventory against the risk of stockouts. Companies should calculate optimal safety stock levels based on demand variability, supplier lead times, and service level requirements. Advanced inventory management systems can automate safety stock calculations and adjustments.
Develop Supplier Partnerships
Building strong relationships with key suppliers enables better pricing, priority allocation during shortages, and improved delivery reliability. Companies should work collaboratively with suppliers on demand planning, inventory management, and quality improvement initiatives. Long-term partnerships often provide cost advantages and operational benefits.
Leverage Technology Solutions
Modern inventory management software provides real-time visibility, automated reordering, and analytics capabilities that significantly improve efficiency. Cloud-based solutions offer scalability and integration with other business systems. RFID and barcode technologies enable accurate tracking and reduce manual errors.
Implement Just-in-Time Delivery
Coordinating supplier deliveries with project timelines reduces inventory holding costs and storage requirements. This approach requires close collaboration with suppliers and accurate project scheduling. Companies should balance just-in-time benefits with the need for buffer stock to handle unexpected delays.
Regular Inventory Reviews and Audits
Conducting periodic inventory reviews identifies slow-moving items, obsolete equipment, and process improvement opportunities. Physical inventory audits ensure system accuracy and identify shrinkage issues. These reviews should include assessment of storage conditions and equipment quality.
Standardize Equipment Specifications
Reducing equipment variety through standardization improves inventory pooling and reduces carrying costs. Companies should work with engineering teams to standardize component specifications across projects while maintaining performance requirements. This approach enables better supplier negotiations and inventory utilization.
Effective solar inventory management represents a critical competitive advantage in the rapidly evolving solar energy industry. Companies that master the complexities of equipment procurement, storage, and distribution can achieve significant cost savings, improved project delivery, and enhanced customer satisfaction. The key lies in implementing comprehensive systems that balance cost control with operational efficiency while maintaining flexibility to adapt to changing market conditions.
Success in solar inventory management requires a holistic approach that integrates demand planning, supplier relationships, technology solutions, and performance measurement. Companies must invest in both technology infrastructure and skilled personnel to manage the unique challenges of solar equipment inventory. As the industry continues to grow and mature, those organizations that develop superior inventory management capabilities will be best positioned to capitalize on emerging opportunities while maintaining profitable operations.
The future of solar inventory management will likely see increased automation, artificial intelligence integration, and supply chain digitalization. Companies that begin implementing these advanced approaches today will build sustainable competitive advantages for long-term success in the dynamic solar energy market. By focusing on continuous improvement and adaptation to industry changes, solar companies can transform inventory management from a cost center into a strategic differentiator that drives business growth and profitability.
Lorem ipsum dolor sit amet, consectetur adipiscing elit. Donec ullamcorper mattis lorem non. Ultrices praesent amet ipsum justo massa. Eu dolor aliquet risus gravida nunc at feugiat consequat purus. Non massa enim vitae duis mattis. Vel in ultricies vel fringilla.
Introduction
Mi tincidunt elit, id quisque ligula ac diam, amet. Vel etiam suspendisse morbi eleifend faucibus eget vestibulum felis. Dictum quis montes, sit sit. Tellus aliquam enim urna, etiam. Mauris posuere vulputate arcu amet, vitae nisi, tellus tincidunt. At feugiat sapien varius id.
Eget quis mi enim, leo lacinia pharetra, semper. Eget in volutpat mollis at volutpat lectus velit, sed auctor. Porttitor fames arcu quis fusce augue enim. Quis at habitant diam at. Suscipit tristique risus, at donec. In turpis vel et quam imperdiet. Ipsum molestie aliquet sodales id est ac volutpat.
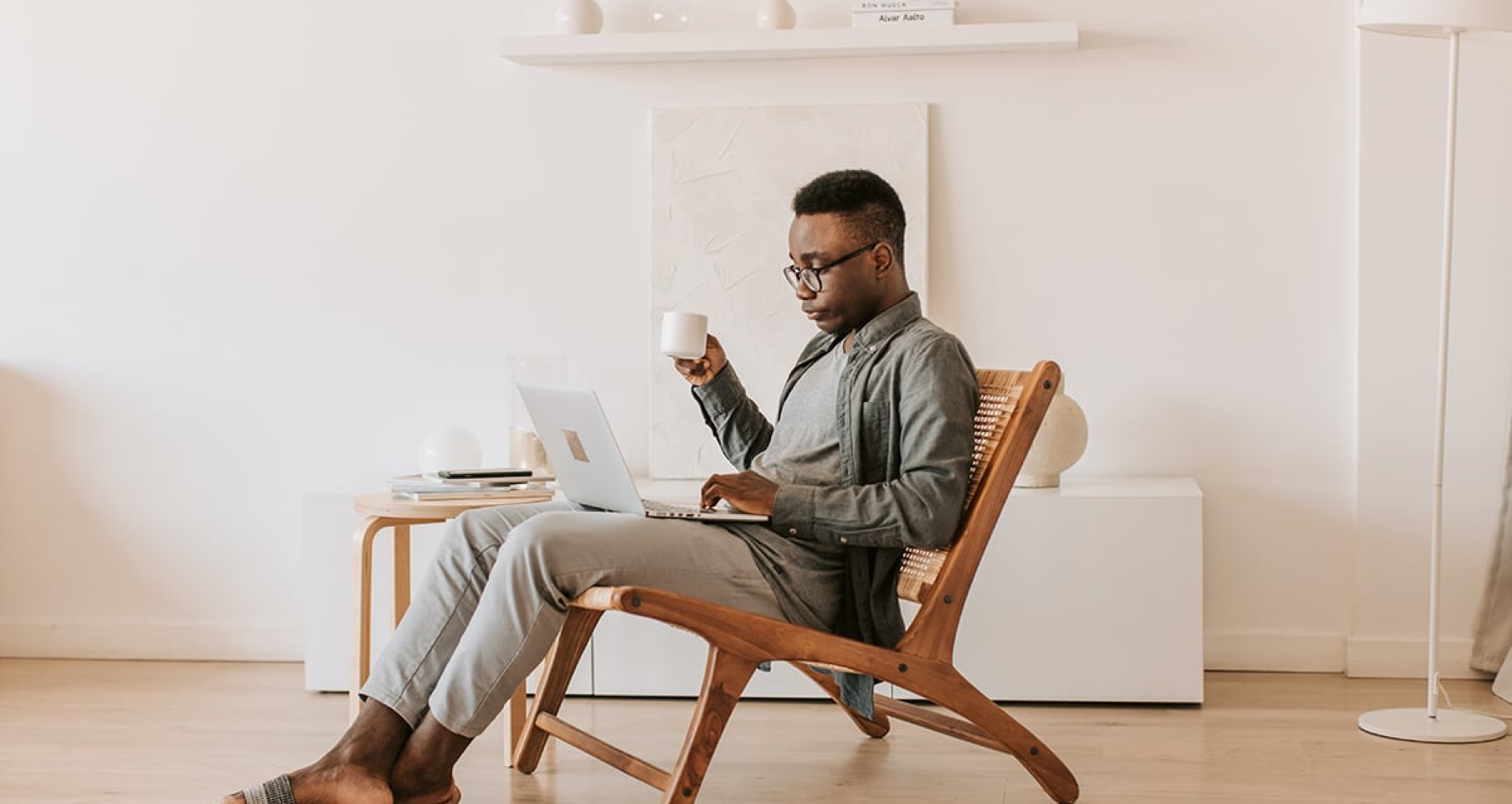

Ipsum sit mattis nulla quam nulla. Gravida id gravida ac enim mauris id. Non pellentesque congue eget consectetur turpis. Sapien, dictum molestie sem tempor. Diam elit, orci, tincidunt aenean tempus. Quis velit eget ut tortor tellus. Sed vel, congue felis elit erat nam nibh orci.

Dolor enim eu tortor urna sed duis nulla. Aliquam vestibulum, nulla odio nisl vitae. In aliquet pellentesque aenean hac vestibulum turpis mi bibendum diam. Tempor integer aliquam in vitae malesuada fringilla.
Elit nisi in eleifend sed nisi. Pulvinar at orci, proin imperdiet commodo consectetur convallis risus. Sed condimentum enim dignissim adipiscing faucibus consequat, urna. Viverra purus et erat auctor aliquam. Risus, volutpat vulputate posuere purus sit congue convallis aliquet. Arcu id augue ut feugiat donec porttitor neque. Mauris, neque ultricies eu vestibulum, bibendum quam lorem id. Dolor lacus, eget nunc lectus in tellus, pharetra, porttitor.
Ipsum sit mattis nulla quam nulla. Gravida id gravida ac enim mauris id. Non pellentesque congue eget consectetur turpis. Sapien, dictum molestie sem tempor. Diam elit, orci, tincidunt aenean tempus. Quis velit eget ut tortor tellus. Sed vel, congue felis elit erat nam nibh orci.
Mi tincidunt elit, id quisque ligula ac diam, amet. Vel etiam suspendisse morbi eleifend faucibus eget vestibulum felis. Dictum quis montes, sit sit. Tellus aliquam enim urna, etiam. Mauris posuere vulputate arcu amet, vitae nisi, tellus tincidunt. At feugiat sapien varius id.
Eget quis mi enim, leo lacinia pharetra, semper. Eget in volutpat mollis at volutpat lectus velit, sed auctor. Porttitor fames arcu quis fusce augue enim. Quis at habitant diam at. Suscipit tristique risus, at donec. In turpis vel et quam imperdiet. Ipsum molestie aliquet sodales id est ac volutpat.
Mi tincidunt elit, id quisque ligula ac diam, amet. Vel etiam suspendisse morbi eleifend faucibus eget vestibulum felis. Dictum quis montes, sit sit. Tellus aliquam enim urna, etiam. Mauris posuere vulputate arcu amet, vitae nisi, tellus tincidunt. At feugiat sapien varius id.
Eget quis mi enim, leo lacinia pharetra, semper. Eget in volutpat mollis at volutpat lectus velit, sed auctor. Porttitor fames arcu quis fusce augue enim. Quis at habitant diam at. Suscipit tristique risus, at donec. In turpis vel et quam imperdiet. Ipsum molestie aliquet sodales id est ac volutpat.
- Lectus id duis vitae porttitor enim gravida morbi.
- Eu turpis posuere semper feugiat volutpat elit, ultrices suspendisse. Auctor vel in vitae placerat.
- Suspendisse maecenas ac donec scelerisque diam sed est duis purus.
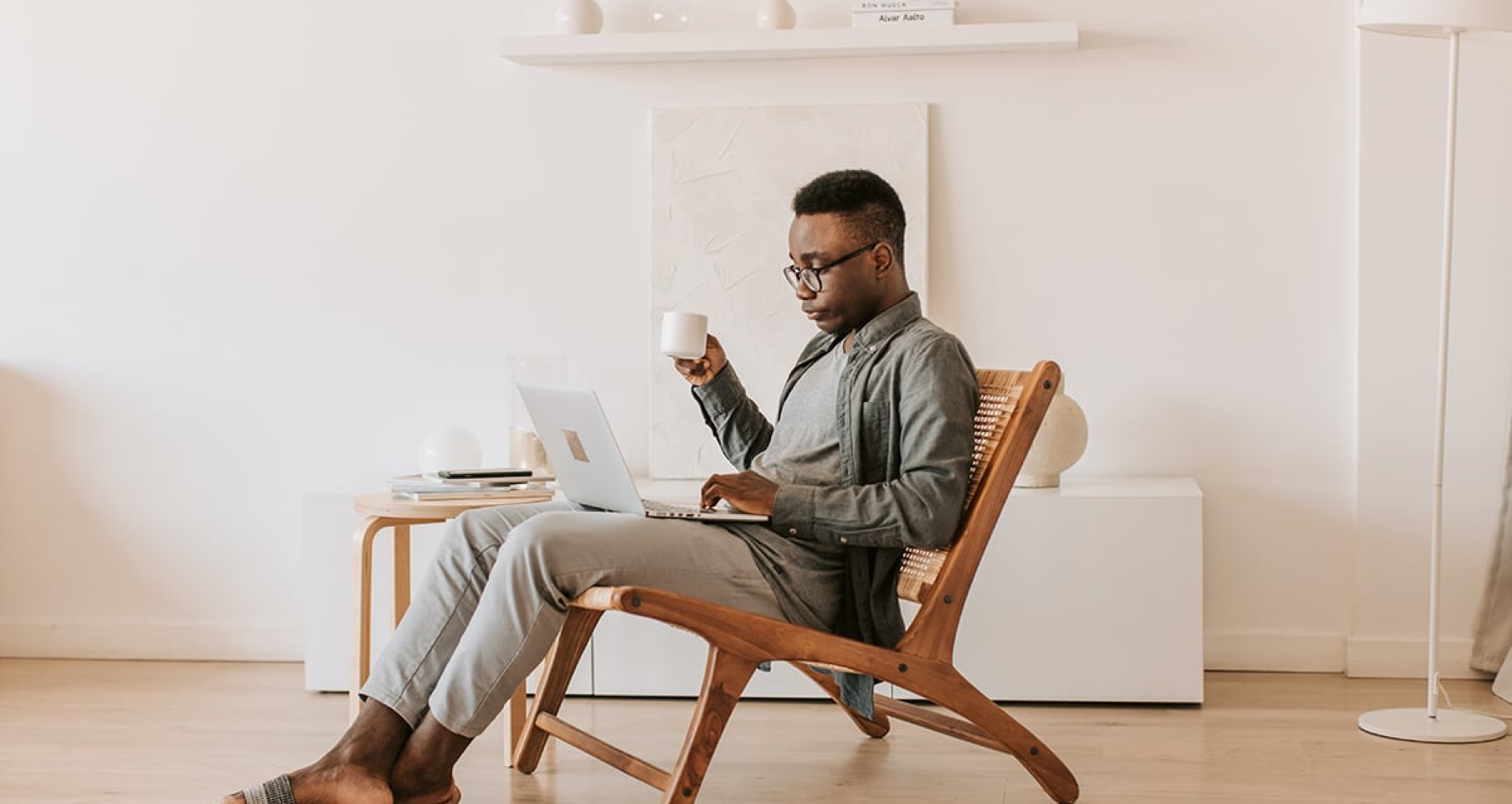

Lectus leo massa amet posuere. Malesuada mattis non convallis quisque. Libero sit et imperdiet bibendum quisque dictum vestibulum in non. Pretium ultricies tempor non est diam. Enim ut enim amet amet integer cursus. Sit ac commodo pretium sed etiam turpis suspendisse at.
Tristique odio senectus nam posuere ornare leo metus, ultricies. Blandit duis ultricies vulputate morbi feugiat cras placerat elit. Aliquam tellus lorem sed ac. Montes, sed mattis pellentesque suscipit accumsan. Cursus viverra aenean magna risus elementum faucibus molestie pellentesque. Arcu ultricies sed mauris vestibulum.